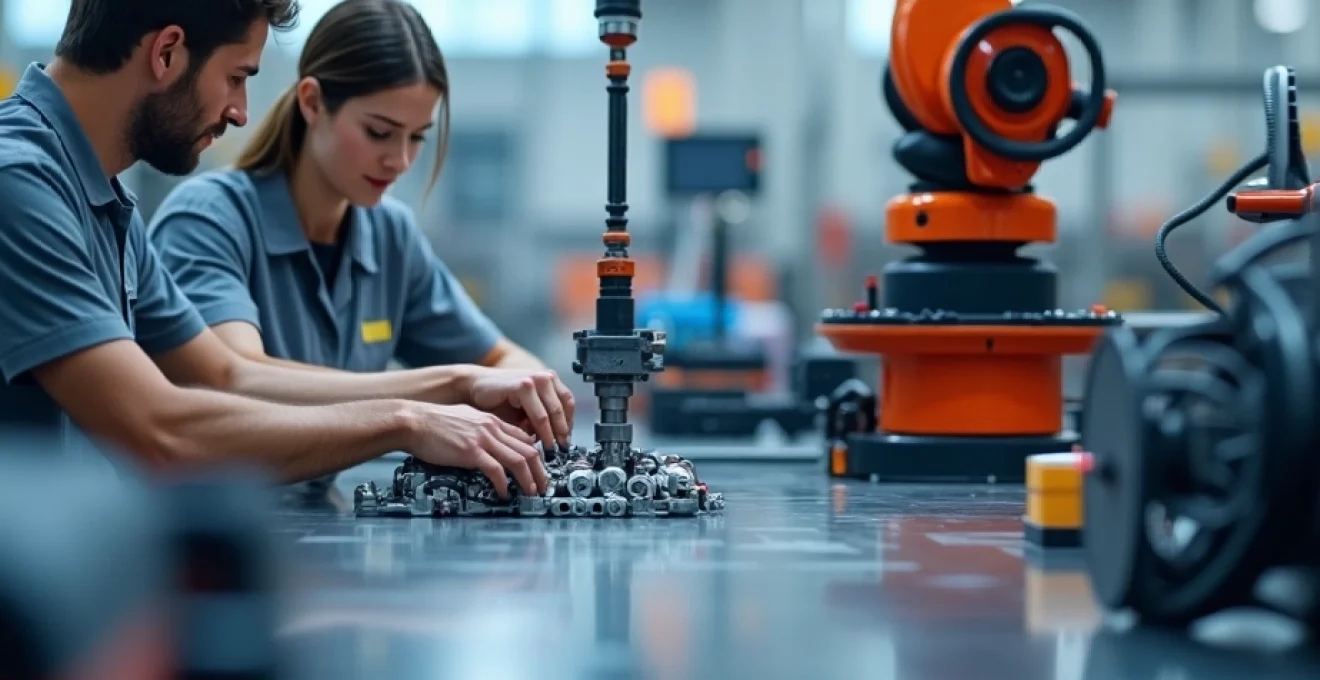
The manufacturing landscape is undergoing a profound transformation, with robotics at the forefront of this industrial revolution. As factories strive for greater efficiency, precision, and adaptability, robotic systems are becoming indispensable tools in the modern production environment. The integration of advanced robotics is reshaping traditional manufacturing processes, offering unprecedented levels of productivity and quality control.
Robotics in manufacturing isn’t just about replacing human workers; it’s about augmenting human capabilities and creating new opportunities for innovation. From automotive assembly lines to electronics production, robots are taking on tasks that were once considered too complex or dangerous for automation. This shift is not only improving output but also redefining the role of human workers in the factory setting.
Robotics enhances manufacturing speed and efficiency
One of the primary reasons robotics is becoming essential in modern manufacturing is its ability to significantly boost speed and efficiency. Robotic systems can perform tasks with a level of consistency and tirelessness that human workers simply cannot match. This enhancement in productivity is crucial for manufacturers looking to stay competitive in a fast-paced global market.
Automated processes boost production output
Automated robotic processes have revolutionized production lines, enabling manufacturers to achieve unprecedented levels of output. By taking over repetitive tasks, robots can work at a constant pace without the need for breaks or shift changes. This continuous operation translates directly into increased production volumes, allowing companies to meet growing demand more effectively.
For instance, in automotive manufacturing, robotic welding systems can perform hundreds of precise welds per hour, far outpacing what human welders could achieve. This dramatic increase in throughput is a game-changer for industries where high-volume production is essential.
Robots operate 24/7 without fatigue
Unlike human workers, robots don’t experience fatigue, which means they can operate around the clock without a decrease in performance. This 24/7 operational capability is particularly valuable in industries where downtime is costly. Continuous production cycles enabled by robotics can lead to significant increases in overall manufacturing output.
Consider a packaging facility that implements robotic systems for sorting and packing products. These robots can work non-stop, maintaining the same level of accuracy and speed throughout their operation. This consistency not only boosts productivity but also reduces the likelihood of errors that might occur due to human fatigue during long shifts.
Streamlined workflows reduce cycle times
Robotic systems excel at optimizing manufacturing workflows, leading to reduced cycle times and improved overall efficiency. By analyzing production processes and identifying bottlenecks, robots can be programmed to perform tasks in the most efficient sequence possible. This streamlining effect can have a ripple impact across the entire production line, significantly reducing the time it takes to manufacture a product from start to finish.
For example, in the electronics industry, robotic pick-and-place machines can assemble circuit boards at speeds that were once thought impossible. These machines can place hundreds of components per minute with pinpoint accuracy, drastically cutting down assembly times and allowing for higher production volumes.
Robotic precision improves product quality
Beyond speed and efficiency, robotics is becoming indispensable in manufacturing due to its unparalleled precision. The ability of robots to perform tasks with exacting accuracy leads to significant improvements in product quality, which is crucial in industries where even minor defects can have serious consequences.
Consistent execution minimizes defects
One of the key advantages of robotic systems is their ability to execute tasks with unwavering consistency. Unlike human workers who may experience variations in performance due to fatigue or distraction, robots perform the same task identically every time. This consistency is vital in minimizing defects and ensuring that every product meets the same high-quality standards.
In the pharmaceutical industry, for instance, robotic systems are used for precise medication dispensing and packaging. The exactitude of these robots ensures that each dose is measured correctly, significantly reducing the risk of errors that could have serious health implications.
Advanced sensors ensure tight tolerances
Modern robotic systems are equipped with advanced sensors that allow them to work within incredibly tight tolerances. These sensors can detect minute variations in materials or positioning, enabling robots to make real-time adjustments to maintain precision. This level of accuracy is particularly important in industries such as aerospace, where components must be manufactured to exacting specifications.
For example, in the production of aircraft engines, robots equipped with laser measurement systems can machine parts to tolerances as fine as a fraction of a millimeter. This precision ensures that engine components fit together perfectly, which is critical for safety and performance in aviation.
Quality control integrated into production
Robotics allows for the integration of quality control directly into the production process. Vision systems and sensors attached to robotic arms can perform inspections at various stages of manufacturing, identifying defects or inconsistencies immediately. This real-time quality assurance helps prevent defective products from progressing through the production line, saving time and resources.
In the automotive industry, robotic vision systems inspect paint finishes for imperfections that might be invisible to the human eye. By catching these flaws early, manufacturers can address quality issues before they become costly problems, ensuring that only flawless products reach the consumer.
Robots perform hazardous manufacturing tasks
One of the most compelling reasons for the adoption of robotics in manufacturing is the ability of robots to take on tasks that are dangerous or harmful to human workers. By relegating hazardous operations to robotic systems, manufacturers can significantly improve workplace safety and reduce the risk of injuries or long-term health issues among their workforce.
In industries such as metalworking or chemical processing, robots can handle materials at extreme temperatures or work with toxic substances without risk. For instance, in foundries, robots are now commonly used for pouring molten metal, a task that exposes human workers to extreme heat and potentially dangerous fumes. By using robots for these operations, manufacturers can protect their employees while maintaining production efficiency.
Moreover, robots can operate in environments that would be inhospitable or impossible for humans to work in for extended periods. This includes areas with high radiation levels, such as in nuclear power plant maintenance, or in extremely cold or hot conditions that would require extensive protective gear for human workers. The use of robots in these scenarios not only ensures safety but also allows for more consistent and prolonged operation in challenging environments.
Robotics in hazardous environments is not just about replacing human workers; it’s about extending human capabilities and creating safer, more efficient industrial processes.
Another significant advantage of using robots for hazardous tasks is the reduction of repetitive strain injuries. Many manufacturing processes involve repetitive motions that can lead to chronic health issues for human workers over time. Robots can perform these repetitive tasks indefinitely without the risk of developing conditions like carpal tunnel syndrome or back problems, which are common in manual manufacturing roles.
Robotics facilitates manufacturing flexibility
In today’s fast-paced market, the ability to quickly adapt to changing consumer demands is crucial for manufacturers. Robotics plays a pivotal role in creating flexible manufacturing environments that can swiftly adjust to new product requirements or production volumes.
Quick changeovers for different products
One of the most significant advantages of modern robotic systems is their ability to switch between different tasks or product lines with minimal downtime. Unlike traditional manufacturing setups that might require extensive retooling or reconfiguration, robots can be reprogrammed quickly to handle new products or variations.
For example, in the consumer electronics industry, where product lifecycles are short and new models are introduced frequently, robotic assembly lines can be reprogrammed overnight to start producing a new smartphone model. This flexibility allows manufacturers to respond rapidly to market trends and maintain a competitive edge.
Modular design allows easy reconfiguration
Many modern robotic systems are designed with modularity in mind, allowing for easy reconfiguration of production lines. This modular approach means that manufacturers can add, remove, or rearrange robotic components to meet changing production needs without overhauling the entire system.
In the automotive industry, modular robotic cells can be quickly reconfigured to accommodate different vehicle models or even entirely different types of vehicles. This flexibility is crucial for manufacturers who need to produce a variety of products on the same production line or quickly switch between different product lines to meet fluctuating demand.
Adaptable to shifting market demands
The adaptability of robotic systems extends beyond just product changes. They can also adjust to varying production volumes, allowing manufacturers to scale their operations up or down in response to market demands. This scalability is particularly valuable in industries with seasonal fluctuations or unpredictable market conditions.
For instance, a food processing plant using robotic packaging systems can easily adjust its output during peak seasons or unexpected surges in demand. The ability to quickly ramp up production without the need for extensive hiring and training of temporary workers provides a significant advantage in managing variable market conditions.
Collaborative robots work alongside human workers
The latest evolution in manufacturing robotics is the rise of collaborative robots, or cobots. These advanced systems are designed to work safely alongside human workers, combining the strengths of both robots and humans to create more efficient and flexible production environments.
Cobots are equipped with sophisticated sensors and safety features that allow them to detect the presence of humans and adjust their behavior accordingly. This means they can operate without the need for safety cages or barriers, making them ideal for environments where space is at a premium or where frequent human interaction is necessary.
One of the key advantages of cobots is their ability to complement human skills rather than replace them entirely. For example, in assembly operations, a cobot might handle the heavy lifting and precise positioning of components, while a human worker performs more delicate tasks that require dexterity and judgment. This collaboration leverages the strengths of both robots and humans, leading to improved overall productivity and quality.
Collaborative robots are not just tools; they are partners in production, enhancing human capabilities and creating new opportunities for workforce development.
The integration of cobots into manufacturing processes also opens up new possibilities for workforce development. As these robots take on repetitive or physically demanding tasks, human workers can focus on higher-value activities that require problem-solving skills, creativity, and complex decision-making. This shift can lead to more engaging and fulfilling roles for workers, potentially improving job satisfaction and retention.
Moreover, the user-friendly nature of many cobot systems means that workers with limited programming experience can often learn to operate and reconfigure these robots. This democratization of robotics technology empowers workers to take a more active role in process improvement and innovation on the factory floor.
As manufacturing continues to evolve, the synergy between human workers and collaborative robots will likely play an increasingly important role in shaping the factories of the future. The flexibility, safety, and efficiency offered by cobots make them an essential component of modern manufacturing strategies, particularly for companies looking to balance automation with the irreplaceable skills of their human workforce.
The integration of robotics into modern manufacturing is not just a trend; it’s a fundamental shift in how products are made. From enhancing speed and efficiency to improving quality and safety, robots are becoming indispensable tools for manufacturers aiming to stay competitive in a global market. As technology continues to advance, the role of robotics in manufacturing will only grow, driving innovation and reshaping the industrial landscape for years to come.